
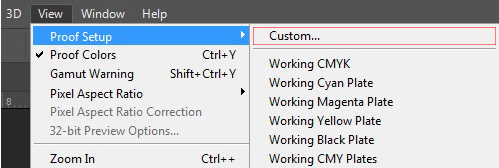
Now that you know why color management is necessary for sublimation printing, let’s look at a few ways this is accomplished. This is why we recommend that you only use high-quality paper.

However, extensive testing has shown that in most cases, good-quality transfer paper does not affect the final color. In extreme circumstances, color correction may be needed for every combination of printer /ink/substrate and transfer paper. With sublimation, these issues need to be addressed for each individual printer and ink combination. This is because of the chemical characteristics of the dye sublimation process, and another reason why color correction is needed. You may also notice that colors of the ink printed on your transfer paper are very different from the final image that is created when heat and pressure are applied. During this “gassing” process certain colors will shift, so the finished product will not look like the original image on the screen. When a dye sublimation transfer sheet is heated and pressed onto a substrate, the ink turns into a gas that bonds with the polymers of the substrate. With dye sublimation, there is another element of the color control process that must be addressed. Color management – or color correction - is the process of adjusting this color transformation so that you can produce the best quality results on your substrate.
How to install icc profile in silhouette software#
In digital product decoration, you design in an additive environment (RGB), and then the printer and software has to convert those colors to work in a subtractive environment (CMYK).

One is additive the other is subtractive. Cyan, magenta and yellow pigments or dyes serve as filters, subtracting varying degrees of red, green and blue from white light to produce a selective gamut of spectral colors.Īs you can see, there is marked difference in how both types of color generation work. Printed products absorb or reflect specific wavelengths of light, unlike a screen that emits light. Although all colors of the visible spectrum can be produced by merging red, green and blue light, monitors can display only a limited gamut (range of color) of the visible spectrum. CMYK (cyan, magenta, yellow and black) is the standard for four-color digital printing.Ĭomputer monitors emit color as RGB light. Conversely, digital printers use anywhere from four to eight ink colors to reproduce the image from your screen. This is because the colors on screens are generated by combinations of three colors: red, green and blue (RGB). The colors you see on your screen will never match the colors in your prints exactly. Though color science can be complex, here are some basic concepts that will help you achieve great color output and repeat business. Understanding how color works in a digital print environment is essential to success in sublimation. The science comes in during the print and press process. The art comes into play when you’re designing what to put on your product. Color Management Basics Every Product Decorator Should KnowĬolor is both an art and science when it comes to digital product decoration.
